From the structure of screens, they can be roughly divided into three parts, which are protective glass, touch screen, and display screen from top to bottom. These three parts need to be bonded.
Summary of Bonding Technologies:
Bonding methods can be divided into three categories: optical bonding, zero bonding, and air gap bonding.
1. Optical bonding/full lamination is also called non-air-gap technology
Optical bonding is a technical process in which the display screen and touch screen are seamlessly and completely bonded together by LOCA or OCA.
Advantages of optical bonding technology:
1. It can isolate the screen from dust and water vapor. The air gap bonding of the screen is easily polluted by dust and water vapor in the environment, which impacts the use of the machine; In the full lamination screens, LOCA or OCA glue has filled the gap. The display panel is closely bonded to the touch screen, so dust and water vapor cannot enter the screen, and the cleanliness of the screen is maintained.
2. Better display effect. Full lamination technology eliminates the air between screens, which can significantly reduce the reflection of light and the loss of transmitted light, thus improving the brightness and enhancing the display effect of the screen.
3. Reduce noise interference. The touch screen is closely integrated with the display panel. In addition to improving the strength, full lamination can effectively reduce the interference caused by noise to touch signals and enhance the smoothness of touching actions.
4. Make the screen thinner. When the touch screen and the display screen are bonded by LOCA, the thickness is only increased by 25 μm-50 μm. It is 0.1 mm-0.7mm thinner than the air gap bonding.
Disadvantages of optical bonding technology:
The process complexity is higher, the production pass rate is low, and the rework is complex; The cost of equipment is high; Higher requirements for the workshop environment.
Classification of full lamination technology:
OCA——optical clear adhesive
The unique adhesive used for cementing transparent optical elements (such as lenses, etc.) has the characteristics of transparency, light transmittance over 90%, good cementing strength, curing at room temperature or medium temperature, and minor curing shrinkage.
At present, it is mainly suitable for small-sized products. Each product needs a new mold, which is expensive, and the bonding is very costly; It contains a photoinitiator and is prone to yellowing; Bubbles are easy to occur at the difference of ink segment; The thickness of small-size products is generally between 100um and 200um. For products with large sizes, the bonding thickness needs to reach 1000um, that is, 1mm. On the one hand, it is due to the interference of large sizes; on the other hand, it is to make up for the unevenness of glass through the thick layer of glue.
Advantages: High production efficiency, uniform thickness, no glue overflow problem, controllable bonding area, no corrosion problem, and simple maintenance.
OCA Process Flow:
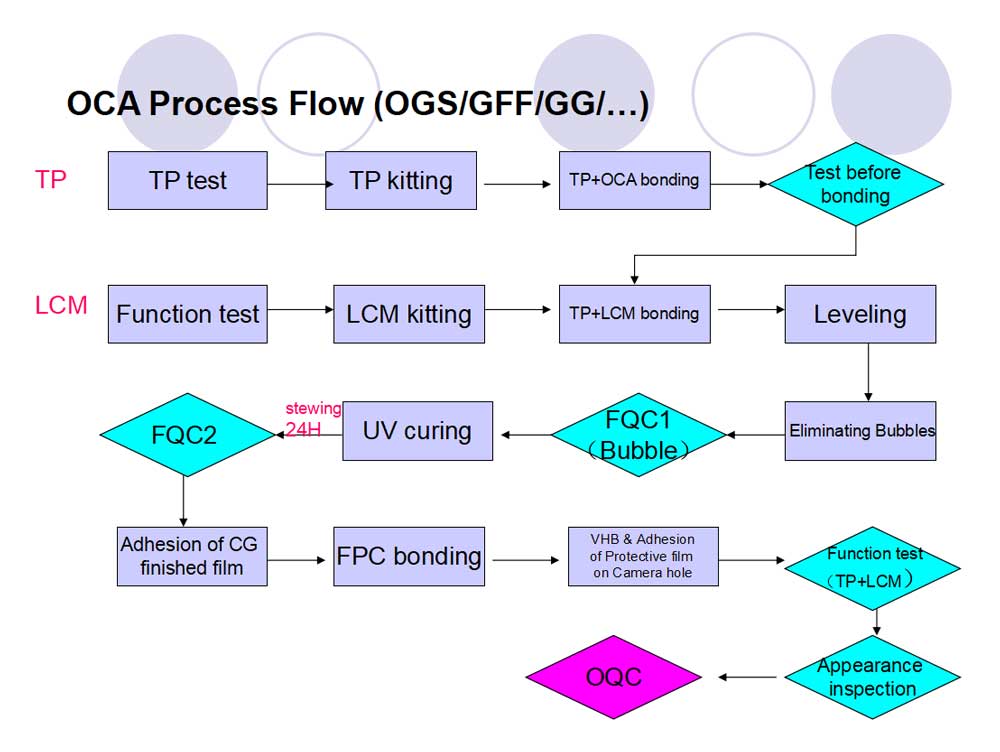
LOCA——liquid optical clear adhesive
Liquid optical clear adhesive is a special adhesive mainly used for bonding transparent optical elements. It is colorless and transparent, with light transmittance over 98% and good bonding strength. It can be cured at a normal temperature or medium temperature. At the same time, it has the characteristics of minor curing shrinkage and yellowing resistance.
It is mainly used in bonding large-size products with a curved surface or complex structures, high ink, or uneven surface. The bonding thickness is 1mm, and the tolerance is about 0.3 mm.
Advantages: It can bond curved surfaces or materials with an uneven surface, which is insensitive to ink thickness, easy to rework, and has a lower cost than OCA.
LOCA bonding operation:
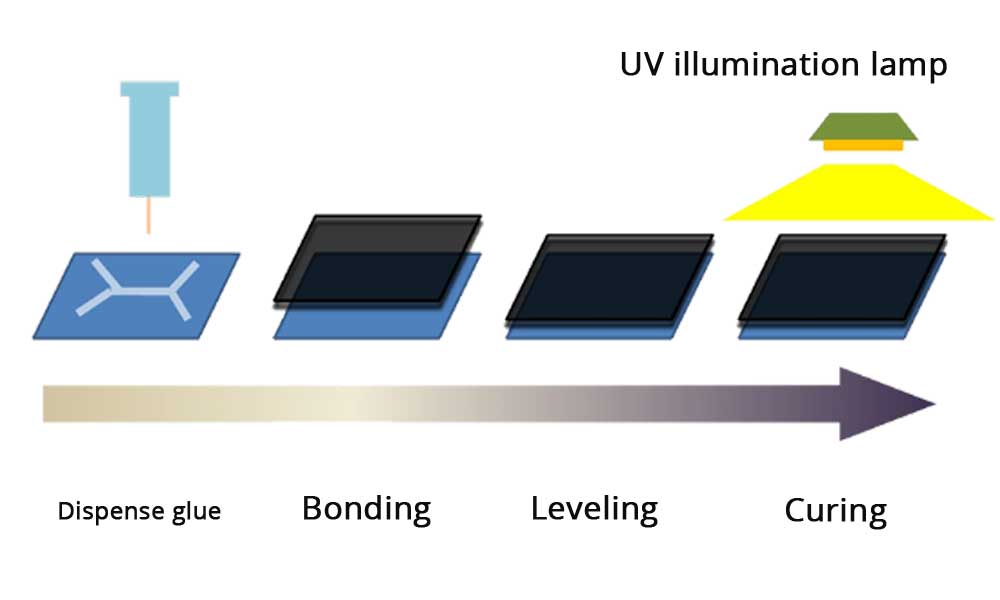
LOCA should be defoamed after sub-packaging and before use, and sub-packaging containers should be reasonably designed and selected. The containers can be used only after standing for 24 hours after transportation and before initial use.
LOCA Process Flow:
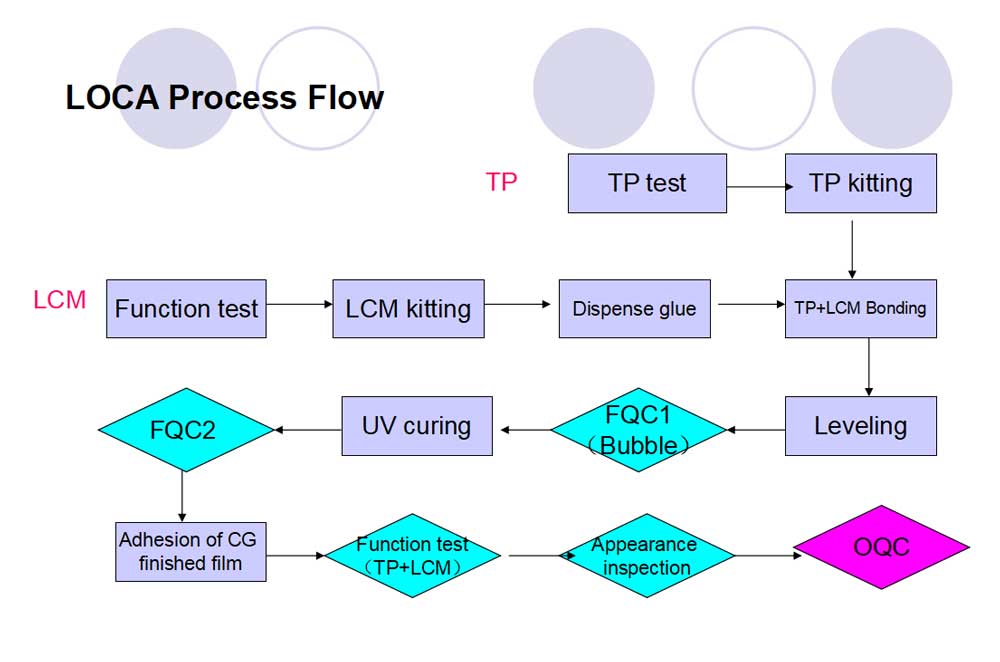
General description
OCA full lamination process is more complicated than LOCA full lamination process because it needs assistance from the die-cutting factory. Currently, many large full lamination manufacturers (including TP and module factories) do not have their own corresponding die-cutting stations. Therefore, the primary supplier of OCA full lamination is a large or medium-sized die-cutting factory. There are many things that could be improved in the coordination between these factories.
Items | LOCA | OCA |
Inventory management | One model can correspond to multiple products | A dedicated mold is needed for each type of product |
Gap filling ability | There is basically no limit to the objects to be bonded | Only the thickness of the gap between 100um to 200um can be filled |
Process complexity | The process flow is simple | More complex |
Bonding pass rate | >90% | <75% |
Scope of application | There is basically no limit to the product size | Suitable for the bonding of small-size products |
Material requirements | Suitable for the bonding of hard materials | No special requirements for the materials of the bonded products |
2. Zero bonding
Zero bonding is a concept that began to emerge in 2018 and has been successfully applied in some manufacturers. Its bonding mode is between full lamination and framed adhesive, which is mainly filling a non-adhesive transparent medium with a refractive index glass equivalent between the touch screen and display screen. On the one hand, there is no gap between the cover lens and the display screen, thus reducing the diffuse reflection and improving the display effect. On the other hand, it is very simple to assemble and maintain because it has no stickiness, and the total cost is low.
3. Air gap bonding or framed adhesive
Framed adhesive is the most widely used way of bonding, simply to fix the four sides of the touch screen and display screen with double-sided adhesive tape. Due to its low cost and simple application, it is favored by small and medium-sized manufacturers. However, an air layer between the display screen and the touch screen results in an unsatisfactory display effect.
Framed adhesive has the advantages of low cost and simple process. However, for large-size modules, the narrower the frame, the thinner the double-sided adhesive tape, and the worse the reliability of the screen. Moreover, if the TP (touch panel) and LCD (liquid crystal display) screen are squeezed, the support of double-sided tape cannot be restored, which will generate a Newton ring, impacting the display effect.
Comparison of 3 touch screen bonding processes
Comparison of 3 touch screen bonding processes |
|||
Bonding type |
Full lamination |
Zero bonding |
Framed adhesive |
Reflection |
The medium is OCA or LOCA with low reflectivity |
The medium is transparent and the reflectivity is low |
The medium is air, and the diffuse reflection is serious |
Moisture proofing |
The medium is optical glue, and there is no water vapor infiltration |
There is a slight gap, and water vapor is easy to enter |
Water vapor easily penetrates from the interface area of double-sided adhesive tape |
Dustproof |
Filled with colloid in the middle, and no dust can enter |
Fine dust may enter |
After vibration, dust is easy to enter |
Cost |
High |
Normal |
Low |
Pass Rate |
85% |
95% |
99% |
Structural strength |
Good |
Good |
Relatively poor |
Display effect |
Excellent |
Good |
Normal |
Visual angle |
150 |
About 140 (no measured data) |
105 |
4. The design code of full lamination and framed adhesive
4.1 Suggestions for full lamination design:
4.1.1 Suggestions for module structure design by bonding:
4.1. 1.1 The upper polarizer of the LCD should be higher than the plastic frame, and the height difference should be greater than 0.05 mm.
4.1.1.2 The bottom of the LCM (liquid crystal module) should be as flat as possible. Backlight hooks should be designed elsewhere. FPC does not need to be bent to the back of LCM and will be bent and attached to it after full lamination.
4.1. 1.3 For products with GG structure, the flatness of CG (cover glass) should be less than 0.15 mm to reduce the risk of bubbles in the bonding process.
4.1. 1.4 The outer edge of the LCD polarizer should be at least 0.8 mm larger than the VA (view area) area of CG (cover glass).
4.1. 1.5 LCM shall avoid the location of TP Shielding FPC and OGS FPC.
4.1. 2 Precision control of LCD by bonding:
4.1. 2.1. The control accuracy distance from the polarizer to LCD-AA (active area) should be less than +/-0.2 mm
4.1. 2.2. The control distance tolerance from the polarizer to the LCD-outer edge should be less than +/-0.3 mm
4.1. 2.3. The control accuracy distance from LCD-AA (active area) to the outer edge of the LCD should be less than +/-0.2 mm
4.1. 2.4. The control accuracy of the LCD outer dimension should be less than 0.15 mm.
4.1. 2.5. The control precision of the polarizer’s outer dimension should be less than 0.15 mm
4.1. 2.6. The control thickness of the LCD module should be less than 0.1 mm
4.1. 2.7. The warpage control should be less than 0.3 mm
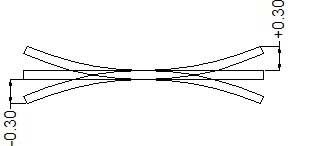
4.1. 3 The requirements for electrical performance in the bonding of TP and LCD:
4.1. 3.1. Under the full lamination scheme, TP is easily interfered by LCD clutter, and the requirements for the anti-interference performance of TP IC are incredibly high. In the early stage of project development, TP IC factory should evaluate the interference of LCD to TP.
4.1.3.2. LCM uses DC (Direct Current)-VCOM, and AC (Alternating Current)-VCOM is not recommended;
4.1. 4. The structural requirements for the whole machine design in bonding:
4.1. 4.1. When designing the whole machine, the warpage in the thickness direction of the LCD should be considered, and at least 0.3 mm space should be reserved.
4.1. 4.2. If the bonding module is stuck to the steel sheet in the mold, the flatness and warping of the steel sheet must be ensured. And it cannot interfere with the back of the LCD to avoid uneven displays such as yellow blocks.
4.1. 4.3. At present, due to the narrow frame and large screen, the TP of the module must have enough bonding force when bonding with the front shell to prevent the module from separating from the front shell during a falling or roller test.
4.1. 4.4. If the frame is too narrow to dispense glue, it is recommended to dispense glue on the side after the TP and LCD module are bonded to avoid the separation of the black-white glue during the LCD drop test; Dispensing glue on the side is shown in the figure below:
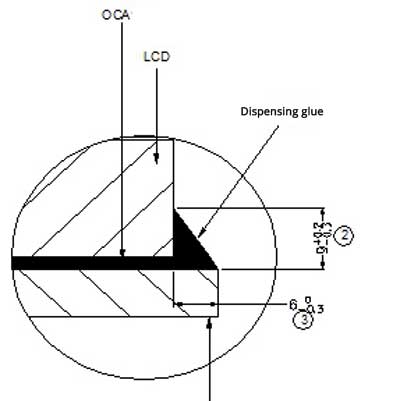
4.2 Design suggestions for framed adhesive:
4.2.1 The double-sided tape should be at least 0.5 mm away from the edge of TP (Touch Panel), CG (cover glass), and VA (view area). It should be at least 1.0 mm away from the LCD (liquid crystal display) AA (active area). It is required that the side view angle should be tilted by 15 degrees to check that foam will not leak.
4.2. 2 By covering the polarizer on each edge with the double-sided tape at least 0.4 mm, the light will not leak.
4.2. 3 For the IC area, the double-sided foam should be more than 0.5 mm on one side to ensure that the IC will not be pressed in the assembly process.
4.2. 4 The distance between the double-sided tape and LCD frame should be 0.1 mm smaller on the left and right sides and 0.15 mm shorter on the upper and lower sides, which is convenient for the positioning of bonding;
4.2.5 At present, framed adhesive is not recommended for OGS TP. Considering that the thickest OGS used by our company is 0.7 mm glass, and the drop performance is relatively poor, so framed adhesive is not recommended.